What is Nanofiber?
Nanofibers are ultrafine fibers that are one-hundredth to one-thousandth the thickness of hair.
There are various types, such as polymer nanofibers made of polypropylene and polyethylene terephthalate. For example, bio-nanofibers such as cellulose, tendons and DNA, carbon nanofibers such as carbon nanotubes, and nanowires made of metal.
Of these, polymer nanofibers have the most potential and have a wide range of applications.
In particular, if the fiber diameter is made ultra-fine (nano-order), new functions not found in fibers of normal thickness will appear. Examples of these new functions are antibacterial properties, ultrafine particle capturing properties, and <the> Slip Flow effect.
Nanofiber is also an eco-friendly material that can be used for masks, filters, water purification, pesticide-free agriculture, etc.
Definition of Nanofibers
Nanofiber is defined as “a fibrous substance with a diameter of 1 nm to 100 nm and a length of 100 times or more the diameter.”
Therefore, carbon nanotubes, DNA, nanocellulose also fall into the category of nanofibers.
By the way, fibers with a diameter of about 1 μm to 10 μm are called microfibers.
Fibers with a diameter of 0.1 μm (100 nm) to 1 μm (1000 nm) don’t have any specific name but they are called submicron fibers for convenience.
However, starting around less than 600 nm (0.6 μm) appears the functionality unique to nanofibers such as antibacterial properties, ultrafine particle capturing properties, and slip flow effect, that are described in “Definition of Nanofibers”. Therefore, we also include submicron fibers in the nanofiber category.
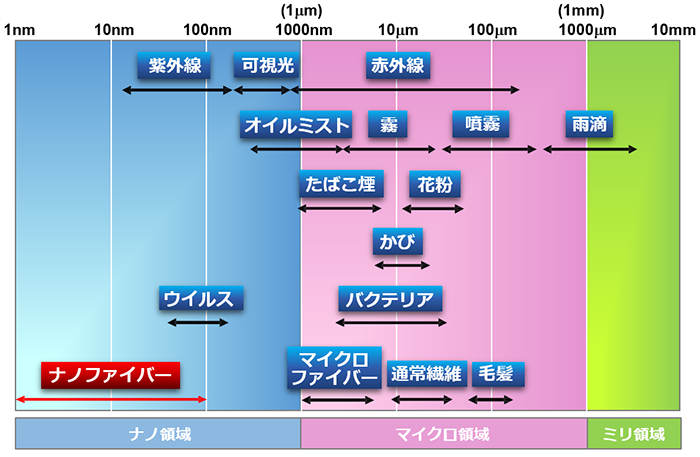
The leading figure of nanofibers in Japan
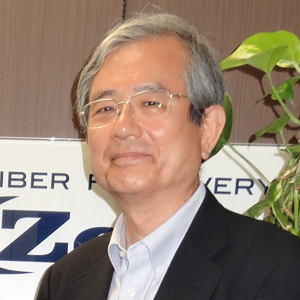
- Chairman of the Nanofiber Society, a specified non-profit organization
- Professor Emeritus, Tokyo Institute of Technology, Doctor of Engineering
- The project leader of a NEDO project, “Project of Advanced Function-Phenotype and Basic Technology Development for New Structural Fiber Material (A national project with total project cost of 5.635 billion yen)
- Director of Zetta Co., Ltd.
The latest manufacturing method
After 15 years of the competition using the electrospinning method, the fiber diameter reached a plateau of 300 nm. Just as the researchers all over the world were not able to break through the limit and disappointment was widespread, Zetta announced a completely new spinning method at ACS as a replacement to the electrospinning method.
The Zetta Spinning method achieved an overwhelming productivity of 20,000 times over its predecessor, a fiber diameter of 100 nm, <and on top of all this, better production safety> and a high safety on top of this – all of this took the nanofiber industry by surprise.
Other manufacturing methods
Until our Zetta-Spinning method was approved as the fourth manufacturing method of nanofibers by the American Chemical Society (ACS), there were only three main manufacturing methods for nanofibers.
- Electrospinning method (electrospinning method)
- Fibers can be spun as thinly as few nm by applying a high voltage to a molecular solution or a molten polymer. Usually, a voltage of several kV or more is used, but the current is small, so energy consumption is also small. Although there are issues such as low productivity, it is the main manufacturing method.
- Composite melt spinning
- The molten polymer is extruded from a special nozzle to obtain fibers with a sea- island structure (similar to cross-sectional area of lotus), and the fibers are considered as nanofibers after being sliced. This method is said to be capable of spinning as thin as about 20 nm. It has issues such as not being applicable to heat-sensitive materials and the need for slicing fiber.
- Melt blow method
- This is a method of obtaining fine fibers by blowing off the molten polymer with hot air while pushing it out of the nozzle. The process is simple as an application of non-woven fabric manufacturing method, but it has issues such as the difficulty to spin 0.5μ or less and the limitation of application to only heat-meltable polymers.
Properties and uses
nanofibers.
- Ultra Specific Surface Area Effect: The surface area per unit weight becomes dramatically larger as it becomes fibrous and thinner. As a result, it has excellent properties such as “molecular recognition” and “adsorption characteristics”, and is expected to be used for biofilters, sensors, fuel cell electrode materials, etc.
- Nano Size Effects: Having a nano size diameter generates effects such as “Fluid dynamics characteristics”, and “optical characteristics”. The effects are expected to be applied for new materials such as an ultra-high performance filter that can completely capture submicron fine particles even with low pressure loss. It can also be used for electronic paper with excellent light transmission because the diameter of the nanofibers is shorter than the wavelength of light and reduces diffused reflection of light to create highly transparent fibers.
- Supramolecular Arrangement Effect: The effect is generated by polymer chains arranged in straight lines, and produces “electrical properties”, “mechanical properties”, “thermal properties”, and more. If conductive atoms and molecules are arranged in a certain order, they’ll create fibers with excellent conductivity, which can be used in mobile fuel cells. In addition, the straight polymer chains create extremely high strength, and the dense structure greatly improves heat resistance. There is an expectation of application for high-performance composite materials in fields that require “light, thin, short or small”.